From Wood To Woven
The Manufacturing Process

Raw Materials
First produced commercially in Mobile, Alabama almost 30 years ago, this wood-based fibre is a forgotten innovation whose time has come..
The main ingredient of bio-fibre is cellulose, a natural polymer found in the cells of all plants. It forms the basis for other plant-derived fibers such as cotton, hemp, and linen. The cellulose for bio-fibre manufacturing is derived from the pulp of hardwood trees. The pulp is typically from a mix of trees chosen for their cellulosic properties such as the color and amount of contaminants. Some common tree species used are eucalyptus, oak and birch. The trees are grown on managed tree farms, generally on land that is not suitable for other agricultural uses. The solvent used in the manufacturing process is an amine oxide, a non toxic sulfactant used in consumer goods such as shampoos and conditioners. Along with water, a finishing agent is also used, and this varies, but is generally a lubricant such as soap or silicone. Bio-fibres are generally dyed with any dyes that are also compatible with cotton.
Preparing the wood pulp
- The hardwood trees grown for bio-fibre production are harvested by loggers and trucked to the mill. At the mill, the trees are cut to 20 ft (6.1m) lengths and debarked by high-pressure jets of water. Next, the logs are fed into a chipper, a machine that chops them into squares little bigger than postage stamps. Mill workers load the chips into a vat of chemical digesters that soften them into a wet pulp. This pulp is washed with water, and may be bleached. Then, it is dried in a huge sheet, and mill workers roll it onto spools. The sheet of cellulose has the consistency of thick poster board paper. The roll of cellulose is enormous, weighing some 500 lb (227 kg).
Dissolving the cellulose
- At the mill, workers unroll several spools of cellulose and break them into one inch squares. The workers then load these squares into a heated, pressurized vessel filled with amine oxide.
Filtering
- After a short time soaking in the solvent, the cellulose dissolves into a clear solution. It is pumped out through a filter, to insure that all the chips are dissolved.
Spinning
- Next, the solution is pumped through spinnerets. These are devices used with a variety of manmade fibers. Something like a showerhead, the spinneret is pierced with small holes, and when the cellulose is forced through it, long strands of fiber come out. The fibers are then immersed in another solution of amine oxide, diluted this time. This sets the fiber strands. Then, they are washed with de-mineralized water.
Drying and finishing
- The bio-fiber next passes to a drying area, where the water is evaporated from it. The strands at this point pass to a finishing area, where a lubricant is applied. This may be a soap or silicone or other agent, depending on the future use of the fiber. This step is basically a detangler, making the future steps of carding and spinning into yarn easier.
Final steps
- The dried, finished fibers are at this stage in a form called tow. Tow is a large untwisted bundle of continuous length filaments. The bundles of tow are taken to a crimper, a machine which compresses the fiber, giving it texture and bulk. The crimped fiber is carded by mechanical carders, which perform an action like combing, to separate and order the strands. The carded strands are cut and baled for shipment to a fabric mill. The entire manufacturing process, from unrolling the raw cellulose to baling the fiber, takes only about two hours. After this, the bio-fibre may be processed in a wide assortment of ways. It may be spun with another fiber, such as cotton or wool. The yarn can be woven or knit like any other fabric, and given a variety of finishes, from cotton soft to silky.
Recovery of the solvent
- The amine oxide used to dissolve the cellulose and set the fiber after spinning is recovered and re-used in the manufacturing process. The dilute solution is evaporated, removing the water, and the amine oxide is routed for re-use in the pressurized vessel in step 2. Ninety-nine percent of the amine oxide is recoverable in the typical cellulose manufacturing process.
Quality Control
Cellulose bio-fibre is only produced at a few plants in the world. These are specially designed, state-of-the-art mills, and quality control is carried out by sophisticated computer monitoring systems. The computers continuously check a variety of key factors, such as the tenacity of the fiber, its color, the denier (a measurement of the fibre's diameter), elongation, moisture level, and level of the finish application. Computers also monitor for "trash" that results when one hole in the spinneret becomes blocked, and the filament comes out splintered or undrawn.
Byproducts/Waste
The manufacture of bio-fibres produces no harmful byproducts and is significantly less toxic and wasteful than the manufacture of other cellulosic fibers. Its principal ingredient, cellulose, is easily obtained from managed tree farms, and the industry has not been accused of poor forestry habits. The amine oxide solvent is non-toxic, and because it is almost completely recycled during manufacturing, it is not released into the environment. Bio-fibre fabrics are also naturally biodegradable and the manufacturing process is environmentally sound because less water and energy is used than in the manufacture of other man made bio-fibers.

Bio-fibre filament in its finished form
The Denim
Sustainable. Durable. Biodegradeable.
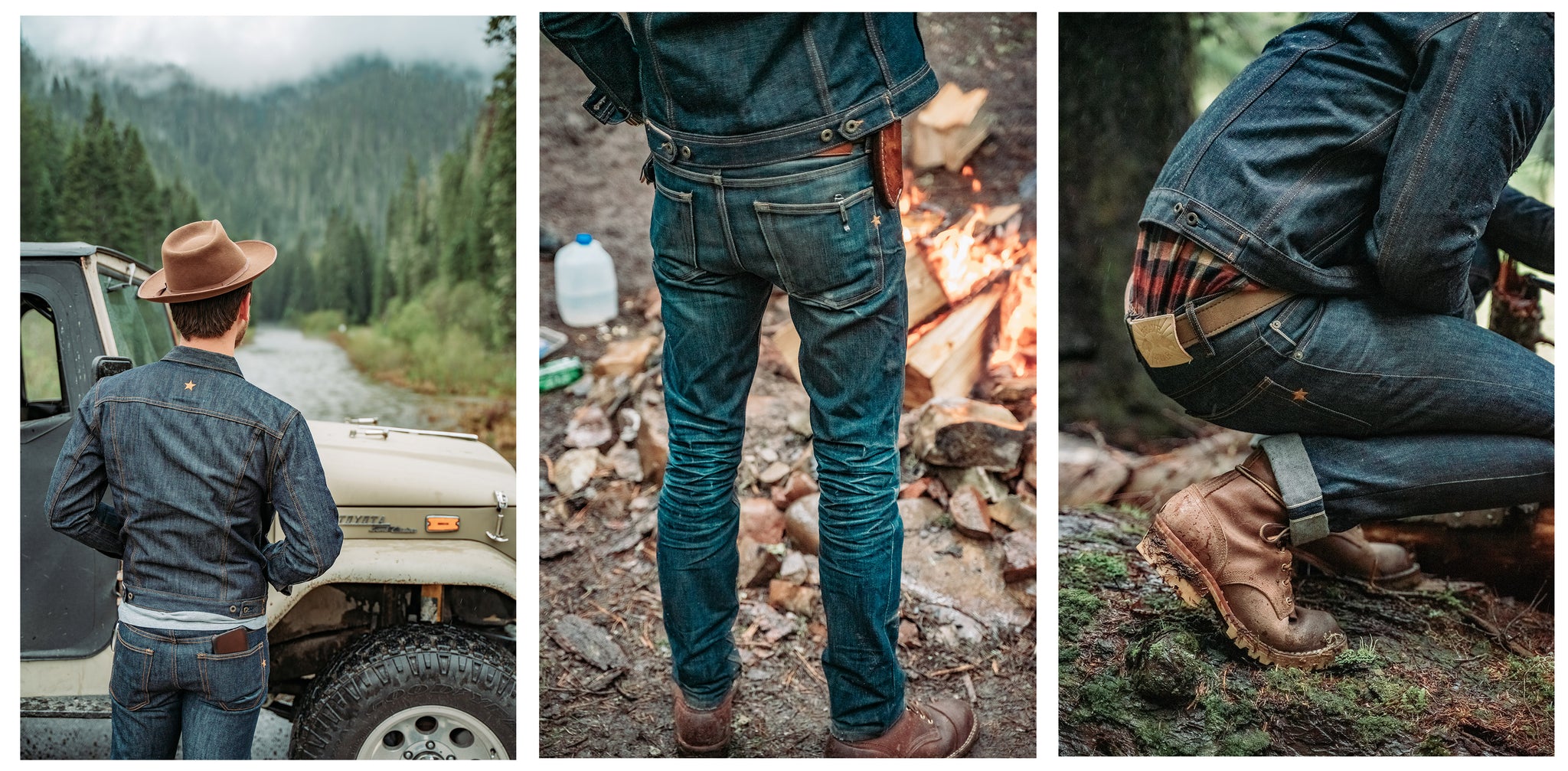
Sustainable
50% LESS WATER 70% LESS CHEMICALS 100% SUSTAINABLEThe manufacture of bio-fibres produces no harmful byproducts, less water and energy is used and is significantly less toxic and wasteful than the manufacture of other cellulosic fibers. Its principal ingredient, cellulose, is easily obtained from managed tree farms, and the industry has not been accused of poor forestry habits. The amine oxide solvent is non-toxic, and because it is almost completely recycled in a closed loop system during manufacturing, it is not released into the environment.
Durable & Breathable
The bio-fibres are extremely strong due to the many nanofibrils (nano fibers) spun together to make yarn. When blended with cotton yarn this denim can take a beating despite it's lighter weight.
Furthermore, airflow and moisture management are two key attributes unique to this hybrid cotton yarn. Moisture wicking and breathability means a pair of jeans that will be comfortable and durable on the most rugged of hikes, long haul road trips or urban bike crawls.
Biodegradable
Bio-fibre fabrics are also naturally biodegradable, so if they ever end up in landfill they will eventually break down to their basic components and blend back in with the earth.

